Introduction
In today’s fast-paced industrial landscape, efficiency and optimisation are paramount. Conveyor systems, the workhorses of countless industries, play a critical role in moving materials swiftly and reliably. Previously, we discussed how to properly maintain and troubleshoot your conveyor system, as to ensure your operation is running smoothly and does not disrupt workflows abruptly.
You need to ensure your conveyor system design operates at its peak, delivering maximum value while being cost effective, minimising downtime, and environmental impact. The answer lies in embracing the latest practices and how you can properly implement a type of conveyor system that leads to increased production and results in the long run.
Understanding Conveyor Designs
Before we discuss the best practices, we should first take a peek into the diverse world of conveyor system designs. Their design goes beyond mere belts and rollers; it’s a symphony of components working together to create the best possible results.
Firstly, belt conveyors, with their continuous loops, excel at high-volume transport of granular materials like sand, grain, and coal. Their belts come in various widths and strengths, accommodating diverse capacities and product characteristics.
Featuring individual rollers, roller conveyors offer versatility for transporting materials of varied shapes and sizes. They cater to boxes, pallets, and even irregularly shaped items, making them ideal for assembly lines and packaging applications. The type of rollers further dictates their functionality and suitability for specific applications.
Additionally, there are vertical conveyors which excel at elevating materials in limited floor space. They come in various designs, such as spiral conveyors, each catering to specific material properties and capacity requirements. Understanding material properties and capacity requirements becomes crucial for choosing the optimal system.
For instance, delicate electronics necessitate gentle handling, prompting vertical conveyors with cushioned platforms. Similarly, high-temperature materials might require heat-resistant buckets or enclosures to prevent damage. Analysing capacity needs helps determine bucket size, motor power, and overall system strength, ensuring smooth operation and avoiding overloads.
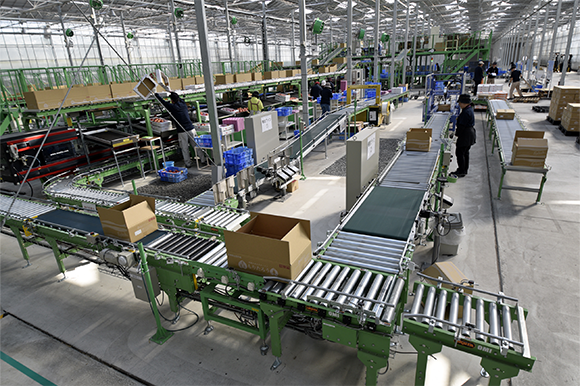
Efficiency & Sustainability
Latest technological advances within the industry demand a focus on both economic and environmental sustainability. Over the last few years, numerous energy-saving technologies have been developed to empower conveyor systems. For example, variable speed drives adjust based on real-time load, significantly reducing energy consumption, particularly in light-load scenarios. Imagine a conveyor system intelligently slowing down when carrying fewer items, saving valuable energy without compromising throughput.
Regenerative braking systems capture kinetic energy during deceleration, feeding it back into the grid. This technology is particularly beneficial for inclined conveyors or systems with frequent stops and starts, transforming wasted energy into a valuable resource.
Materials selection also plays a key role. Environmentally friendly options like recycled steel for frames and bio-based lubricants minimise environmental impact. Additionally, smart control systems and data analytics provide valuable insights for optimising performance and identifying areas for improvement. Imagine a system that analyses historical data to predict belt wear and schedule maintenance proactively, preventing downtime and unnecessary part replacements.

Safety & Reliability
Safety can never be an afterthought. Adherence to stringent safety regulations and standards is paramount, encompassing guarding around pinch points, emergency stop buttons readily accessible, and proper access control to prevent unauthorised entry.
Predictive maintenance strategies utilise sensor data and AI to anticipate potential issues before they occur, preventing costly downtime and ensuring operator safety. Imagine a system that alerts technicians to a misaligned bearing before it causes belt damage, minimising disruptions and protecting vital equipment.
Implementing condition monitoring systems with vibration sensors and thermal cameras further enhances preventative maintenance. These systems continuously monitor key parameters, providing early warnings of potential failures, allowing technicians to address issues before they escalate.
Integration & Scalability
In today’s dynamic environment, flexibility is key. Conveyor systems must seamlessly integrate with other systems and processes within your facility. Imagine a conveyor system that automatically interfaces with robots for loading and unloading, streamlining material handling and optimising production flow.
Modular designs allow for easy expansion and modification, adapting to changing needs. Imagine easily adding additional sections to your conveyor system as your production volume increases, ensuring adaptability and avoiding costly system replacements.
Digital twins, virtual representations of your physical system, enable advanced planning and testing of future configurations. Imagine simulating different layouts and conveyor types in a virtual environment before making real-world changes, minimising risk and ensuring smooth transitions as your operations evolve.

User-Centric Design
Ergonomic considerations prioritise operator comfort and safety, reducing fatigue and risk of injury. You should consider conveyor systems with adjustable workstations and control panels positioned for optimal reach, minimising strain and promoting operator well-being.
Intuitive controls and user interfaces simplify operation, minimising training time and increasing efficiency. Imagine easy-to-understand control panels with clear instructions and visual indicators, empowering operators to quickly grasp system functionality and respond to potential issues.
Conclusion
By incorporating these 2024 best practices into your conveyor system design, you can achieve peak efficiency, prioritise operator safety, ensure reliability, and prepare for future growth. Consulting with experienced professionals is crucial to tailor these practices to your specific needs and industry regulations.
Moving forward, the future of conveyor system design will develop further. Expect advancements in automation, artificial intelligence, and predictive maintenance, leading to even smarter and more efficient systems. By embracing these innovations and adhering to best practices, you can ensure your conveyor system remains a valuable asset for your operations, today and tomorrow.